API (Active Pharmaceutical Ingredients) and Excipients
API: Any substance or mixture of substances intended to be used in the manufacture of a pharmaceutical dosage form and that, when so used, becomes an active ingredient of that pharmaceutical dosage form. Such substances are intended to furnish pharmacological activity or another direct effect in the diagnosis, cure, mitigation, treatment, or prevention of disease or to affect the structure and function of the body.
Excipients
Excipients have been defined as inert substances used as vehicles and diluents for drugs. An excipient is a constituent of a medicine other than the active substance, added in the formulation for a specific purpose. While most excipients are considered inactive, some can have a known action or effect in certain circumstances. These must be declared in the labeling and package leaflet of the medicine for its safe use.
Pharmaceutical Excipients are crucial to drug delivery within the body. Generally, an excipient has no medicinal properties. Its standard purpose is to streamline the manufacture of the drug product and ultimately facilitate the physiological absorption of the drug. Excipients might aid in lubricity, flowability, disintegration, and taste and may confer some form of antimicrobial function. Selecting the appropriate excipient to support the design of your pharmaceutical formulation is an important step in the drug manufacturing process.
The procedure of General Precautions for the Sensitivity of API (Active Pharmaceutical Ingredients) and Excipients :
Based on the sensitivity of Active Pharmaceutical ingredients like LIGHT SENSITIVITY, MOISTURE SENSITIVITY, AIR, and HEAT SENSITIVITY precautions are to be followed.
QUALITY MANAGEMENT SYSTEMS IN PHARMA
General Precautions for Light-Sensitive Raw Material
Dispense the material under sodium light and into a black poly-bag /Aluminum bag.
All the processes (viz. Sizing, Mixing, granulation, compression, coating, filling and packing, and QC testing) shall be done under sodium Lamp or subdued light.
Bulk solution/granules for QC testing shall be sampled in amber-colored vials/Bottles or black Poly-bag / Aluminum bags only.
Before line clearance, QA must check that the sodium lamp is ON and/or the congenital lights are off.
QC shall ensure the intactness of bulk sample vials/bags/bottles until the sample is tested.
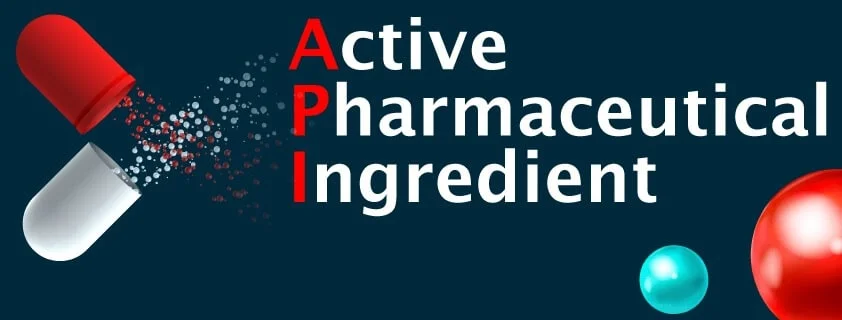
General Precautions for Moisture Sensitive Material.
Dispense the material into black/aluminum bag.
RH of the processing area must be less than 50%(In normal conditions), less than 40% (for the hygroscopic product), and less than 20% (for the highly hygroscopic product) which shall be achieved by means of chilling water so as to have low-temperature low RH air (As per the definition of absolute humidity and RH).
Use only air-tight containers labeled with ‘FOR HYGROSCOPIC PRODUCT’ and put silica bags and desiccants.
Hold time for each process viz. granulation, compression, coating, and packing shall be kept minimum.
Before line clearance, QA must monitor the temperature and RH of the process area as well as actual hold time vs. specified hold time between two processes.
Do not keep drums/containers in open condition unnecessarily during processes.
LOD of bulk shall be achieved minimum.
Bulk granules for QC testing shall be sampled in double aluminum bags only.
QC shall ensure the intactness of the bulk sample bag until the sample is tested.
Highly sensitive API shall have a retest period biyearly.
General Precautions for Air sensitive molecules.
Dispense the material after and before nitrogen flushing into the dispensing container.
D.O. content of bulk solution must be less than 3.0 (can be lesser as per product specific) and to be checked before the solution is kept in a closed container.
Use only air-tight containers labeled with ‘FOR HYGROSCOPIC PRODUCT’ for tablets/capsules.
Hold time for each process shall be kept minimum.
Do not keep drums/containers in open condition unnecessarily during processes.
Each container/tank shall be flushed with nitrogen before filling and have a nitrogen blanket after filling.
QC shall ensure the intactness of the bulk sample vial until the sample is tested.
Highly sensitive API shall have a retest period at a higher frequency.
General Precautions for heat-sensitive material.
Hold time for each process shall be kept minimum.
Before line clearance, QA must monitor the temperature and RH of the process area as well as actual hold time vs. specified hold time between two processes.
Drying shall be done at recommended temperature.
The blister machine temperature set value shall be kept minimum.
Highly sensitive API shall have a retest period at a higher frequency.